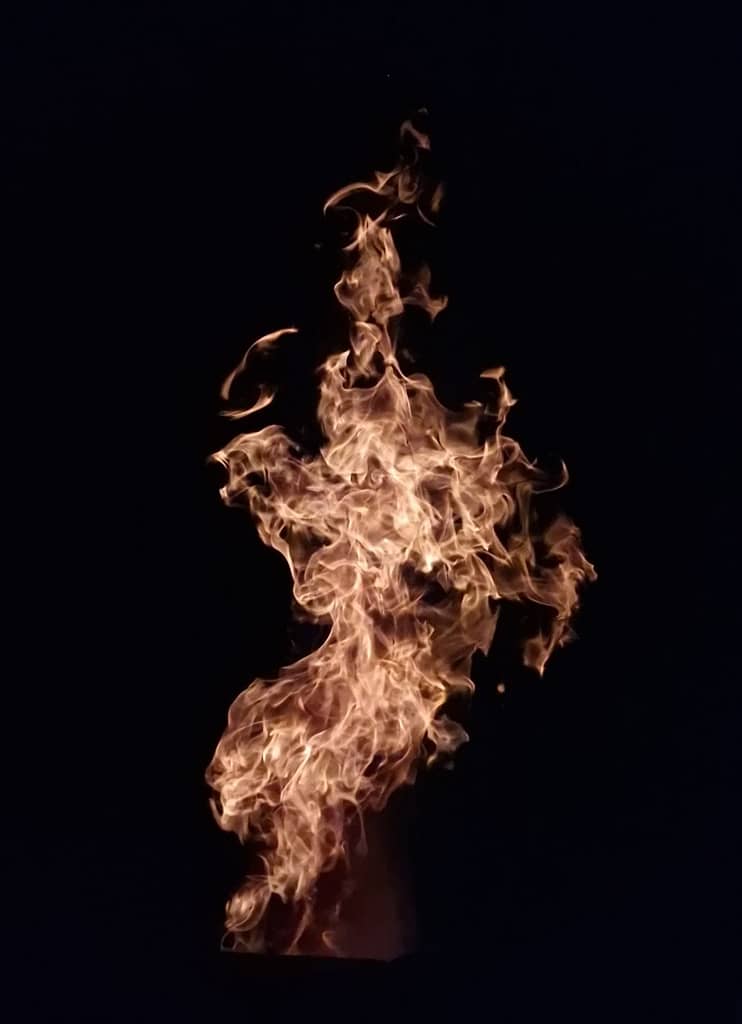
Burn consistently in a wood-fired pottery kiln
600 – 1300 degrees Celsius is the most common temperature range for traditional ceramics. This covers pit firing in one end (600) to stoneware in the other (1250-1300). To reach the highest temperatures you need to burn consistently in a wood-fired pottery kiln, for this; you need both a plan and a schedule. Understanding the combustion processes is absolutely a plus, it is both complex and at the same time as simple as adding dry logs. This text describes the firing range in the kiln linked here but can apply to any kind of ceramic kiln.
https://www.woodfireceramic.com/kilns-horizontal-stack-bricks/
The firing range:
0 – 150 degrees. Take it easy here. Only burn bone-dry clay, use an hour maybe two to get the last moister out of your pots. This is called candeling and it’s done with a small flame. If my work cracks it’s always here at 100 degrees where water turns to steam.
150 – 600 degrees. No need to hold back anymore, get the kiln burning. You reach 600 degrees as long you have enough wood. Even the most poorly constructed kiln should reach 500-600 degrees Celsius, but it can take some time since you also need to heat the kiln, not only what’s in it. A mid-size campfire with a lot of embers (or your house woodstove) reaches 500-600 degrees between the logs, just enough for clay to sinter.
Read about sinter clay in a woodstove here:
https://www.woodfireceramic.com/burning-ceramics-in-a-wood-stove
600 – 800 degrees. Now the clay has sintered into ceramic. Only smoke comes out of the chimney before 600 degrees. Maybe some sparks from time to time, but you never see flames. From here, you need to fire steadily until the length of the flames increases. First, the flames climb up in the ceramic chamber, so the flames start licking out of the chimney. At 800 degrees, the kiln is hot enough to “draw” the flames all the way through the kiln and out the pipe. And the flames will continue to dance out of the chimney with dark red colors. If you fire steadily with dry wood, it’s quite simple to reach 800 degrees in this kiln if you add an extra hour or two.
From 800 degrees things start to be harder. If the temperature won’t continue up – no matter what, we say the kiln is stalling. Stalling is your kiln holding back, and it’s related to either how the kiln is constructed, how you fire your kiln or your fuel. It’s easier to improve your firing technique than to start redesigning your kiln of course, and often you can make wonders with the right technique. When it comes to fuel; save your dryest, best-quality wood for the highest temperatures.
Fire theory:
When you fire up wood, the wood gets “cooked” by the heat until it releases smoke, smoke is unburned wood gases, and you can consider smoke as potential energy. Black smoke out of your chimney = wasting energy, which means you are not burning effectively. Another thing to remember is that fire uses energy to evaporate water bound in the wood, so adding too much wood to the kiln, actually lowers the temperature for a shorter or longer time. Wood burned from the surface and in, so it makes sense to use big chunks of wood in the beginning, and smaller pieces when the temperature is high. The wood gases always burn with long flames.
To increase the temperature; it’s as important to control what is lowering the temperature, as well as master what raising it.
Temperature-thieves:
- Evaporation of bound water – Don’t fire with large logs, splitting them into thin sticks to increase the surface. Big logs are well-suited for steady burning over a long time, great for heating up a house. But even the dryest wood contains 10-15% moisture. So in a ceramic kiln, you want to add small pieces of wood that quickly release energy and don’t lower the temperature while evaporating water from big chunks of wood.
- Cold air – The kiln needs a lot of air and a good draft to burn properly, hot air! Cold air straight into the ceramic chamber will lower the temperature, and make it more difficult for the temperature to climb. You need to draw the air through the ventilation shaft (called secondary air), up through the fire, to get heated up before it enters the ceramic chamber.
- Insufficient oxygen flow – Your fire needs oxygen, but it is fed on air. The air contains approximately 78 percent nitrogen, meaning 3/4 of the air passing through your kiln without adding any kind of value, only 1/4 of the air will be accessible for the fire. When planning the kiln consider you need 4 times more air than you first thought.
- Insulation – Cannot be described as an energy-thief, though you will use a considerable amount of energy to heat up the kiln itself. Insulation insulates, and that’s a good thing. But a good insulator also needs a long time to heat up, and you won’t reach the temperature on your goods before your inside kiln walls have the same temperature. As a comparison, primitive pit firing puts the goods directly on the ground and stacks wood all around it, since the flames are hot enough in themselves to sinter clay to ceramic, this way there are no kiln walls that need to be heated first.
From 800 degrees you need to fire more systematically:
- Fire with thin sticks and add energy little by little, not too much at once, since big chunks of wood will lower the temperature for a while.
- Keep the air ventilation shaft under the firebox with enough embers to heat up the air before it enters the fire chamber, but not so much that it blocks the airflow. Regularly remove embers, charcoal, and ash from the air ventilation shaft. The kiln needs a lot of hot air coming up from under the flames.
- Constant firing by developing your own interval scheme as you go (2 sticks every 5 minutes til you reach 900, 2 sticks every 3 minutes from 900 to 1050 for example).
- Don’t be afraid to adjust your interval scheme based on your progress and the kiln’s behavior: Wind, rain, type of wood, what time of the year, and many other factors will affect your time schedule.
800 – 900 degrees – Thick, black smoke is coming out of my pipe (and black smoke = unburned wood gases = unused energy). So why can unused energy pass through my glowing read kiln without igniting? Because it cannot burn without oxygen. The oxygen flow wasn’t sufficient or I added too much wood at once, and the fire used all the oxygen in the kiln. It’s interesting to see how the flames from the pipe “climb” up and start burning the smoke as soon as it leaves the pipe (and oxygen is once again accessible). Remember that flames climbing up in the smoke both look and feel intense, but it means you are wasting energy, and your kiln is getting colder.
900 – 1050 – At 900 degrees and higher the flames are dancing lively half a meter out of the chimney, the color changed from dark red to bright yellow. I achieved nearly smoke-free firing when following my scheme and fired correctly (2 sticks every 3 minutes).
1050 – 1300 – I stop at 1050 degrees Celsius, if you are interested in higher temperatures for porcelain and stoneware, there is nothing stopping you, and I guess 1200 degrees can be possible with this kiln, good luck experimenting further!
Finally Max temperature!
Even if your digital thermometer says you have reached your temperature, remember that the flames find the easiest path, heat spreads unevenly in a wood-fired kiln. This means that tighter-packed areas can need another 30 minutes to reach max-temperature.
Some observations at the end:
– Burn consistently in a wood-fired pottery kiln is the key to success
– When the kiln reached 1020 degrees I measured 600 at the end of the chimney
– When closed down the kiln, it rapidly dropped 150 degrees
– Firing from 150 to 1020 degrees Celsius took me 5 hours
– After a rainfall, the bricks are waterlogged, it takes extra hours to dry the kiln (and depending on your brick they can crack (violently) too)
Want to learn more? See the book overview here:
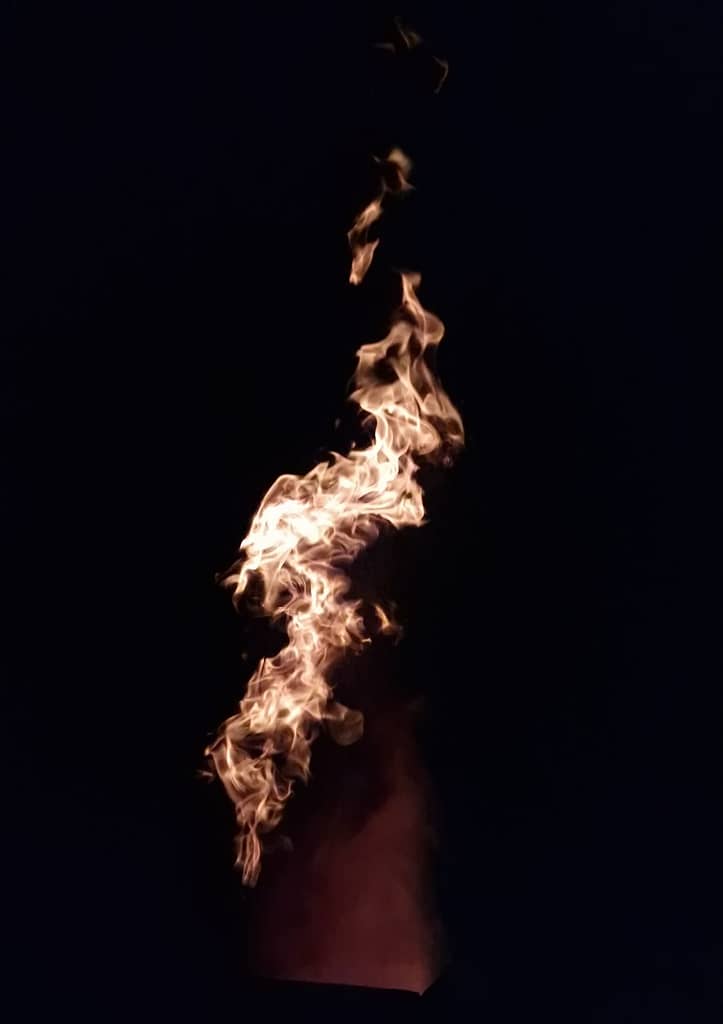
In the picture round, hot, dark, flames are coming from the pipe. All the oxygen in the kiln is consumed so both flames and un-burned wood gases come out of the pipe together. All it needs to burn is available free oxygen, and a spark to ignite it, and the flames start to “climb up” and burn the wood gases as it rise from the pipe.
Read what other say about a fire schedule:
https://www.oxfordclay.co.uk/blog-1/how-to-fire-pottery-what-is-a-kiln-firing-schedule